Company celebrates shipment of
Hydro-to-CathodeĀ® precursor (pCAM) and cathode active
materials (CAM) for use in a heavy duty lithium-ion battery
application
WESTBOROUGH, Mass., June 19,
2024 /PRNewswire/ -- In a milestone for the U.S.
battery materials industry, Ascend Elements recently shipped
decarbonized cathode materials to Freudenberg e-Power Systems, one
of the world's leading suppliers of emissions-neutral energy
solutions for heavy-duty applications. The shipment is notable as
one of North America's first
deliveries of engineered cathode materials for a specific battery
application as part of a commercial vehicle validation and launch
process. Cathode materials made from recycled battery metals can
help EV battery manufacturers qualify for U.S. tax credits under
the Inflation Reduction Act (IRA).
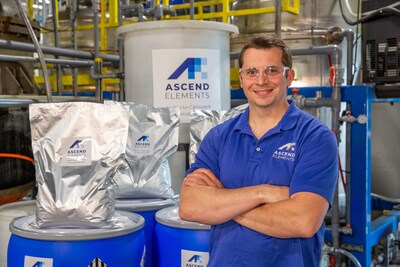
"Battery manufacturers in the United
States are starting to use engineered battery materials that
are made in America from recycled metals," said Eric Gratz, Ph.D., CTO and Co-founder of Ascend
Elements. "Engineered cathode material is normally made in
Asia using material from mined
sources. Now we're making it domestically from recycled EV
batteries and production scrap while generating just half the
carbon footprint."
Ascend Elements uses a patented process known as
Hydro-to-CathodeĀ® direct precursor synthesis to manufacture NMC
pCAM and CAM from used lithium-ion batteries and battery
manufacturing scrap. The closed-loop process eliminates up to 15
intermediary steps in the traditional cathode manufacturing process
and provides significant economic and carbon-reduction benefits. A
recent life cycle assessment conducted by an independent
third-party found Ascend Elements' Hydro-to-CathodeĀ® process
produces EV battery cathode material at a 49% reduction in carbon
emissions compared to traditional cathode manufacturing processes.
By 2030, the company aims to achieve a 90% reduction in carbon
footprint for its decarbonized cathode products.
Since cathode material is the single largest contributor to a
lithium-ion battery cell's carbon footprint, Ascend Elements'
low-carbon cathode material will have a dramatic impact on
Freudenberg e-Power Systems' batteries.
The shipment of pCAM material was engineered and manufactured at
the Ascend Elements pilot facility in Westborough, Mass. The materials will be
sintered and finished as CAM at the Ascend Elements location in
Novi, Mich. before shipment to
Freudenberg e-Power Systems at the XALT Energy plant in
Midland, Mich.
"This is a relatively small shipment in relation to the intended
full-scale commercial program, but it's an important milestone for
Ascend Elements and the U.S. battery materials industry," Gratz
said.
Freudenberg e-Power Systems is proving to be a pioneer in the
lithium-ion battery industry. Ascend Elements' engineers
worked closely with Freudenberg e-Power Systems for over a year to
engineer and manufacture the low-carbon cathode material to
particularly high-performance requirements for lifetime, charge
time, and safety.
"We're very proud to be one of the first to use recycled sources
for our cathode material that powers buses and trucks across the
country. The partnership with Ascend Elements underscores our
ambitions not only to lower the carbon footprint for our customers
but also in our own supply chain and materials," said Lisa McKenzie, President and General Manager of
Battery Systems at Freudenberg e-Power Systems.
Several peer-reviewed studies have shown Ascend Elements'
recycled battery materials perform as well as similar materials
made from virgin (or mined) sources. In fact, Freudenberg tested
Ascend Elements' customized cathode product extensively and found
it to have truly exceptional cycle-life results while achieving
best-in-class safety.
While this shipment of material was made in Massachusetts and finished in Michigan, Ascend Elements continues building a
$1 billion advanced manufacturing
campus in Hopkinsville, Kentucky.
Scheduled to begin operations in early 2025, the
1-million-square-foot Apex 1 facility will eventually produce
enough pCAM and CAM for 750,000 EVs per year.
In addition to the CAM deal with Freudenberg, Ascend Elements
landed a $1 billion contract to
manufacture sustainable pCAM for a major U.S.-based company in
June 2023. Commercial-scale shipments
of material to the undisclosed customer will begin in Q1 2025.
Based in Westborough,
Massachusetts, Ascend Elements is a leading provider of
sustainable, closed-loop battery material solutions. From EV
battery recycling to commercial-scale production of lithium
carbonate and NMC precursor (pCAM) and cathode active materials
(CAM), Ascend Elements is revolutionizing the production of
sustainable lithium-ion battery materials.
View original content to download
multimedia:https://www.prnewswire.com/news-releases/ascend-elements-pioneers-us-battery-materials-industry-with-sustainable-cathode-materials-for-a-commercial-li-ion-battery-application-302176317.html
SOURCE Ascend Elements